Flash Defect
Defects
Excess cast material, often accompanied by dimensional deviations, known as flash.
Cause
A combination of high metal temperature, poor die fit, and inadequate machine locking during high-pressure casting.
Corrections
- Verify die fit at operating temperature: Inspect die alignment and gaps using bluing or other methods while the die is at operating temperature.
- Assess machine locking conditions:
- Equalize tie bar load: Balance the load distribution between tie bars to prevent uneven pressure.
- Inspect machine components: Check for wear in linkages, tie bar bushings, and movable platen shoes. Ensure platens are flat and not bent, the die is properly aligned, and tie bar nuts are tightened securely.
- Center die opening force on the machine: Calculate the center of load and distribute the load evenly across all tie bars to prevent die deflection.
- Optimize metal pressure:
- Maintain static metal pressure in the 3000 to 6000 psi range: Control static pressure within the recommended range.
- Manage intensified metal pressure in the 7000 to 12,000 psi range: Carefully control intensified pressure, ensuring consistency.
- Address high impact spikes: Investigate and mitigate causes of excessive impact spikes, such as accumulator issues.
- Ensure consistent intensifier control: Maintain consistent intensifier operation, preventing variations in pressure application.
- Regulate die and casting thermal conditions:
- Eliminate uneven heating: Identify and address hot spots in the casting or die, which can cause uneven die expansion.
- Provide adequate cooling: Implement cooling systems for hotter areas, such as the biscuit block, sprue, or sleeve, to prevent excessive expansion.
- Avoid heavy sections on the parting line: Minimize the presence of heavy casting sections on the parting line in hot areas of the die.
- Stabilize operating conditions: Maintain consistent die temperature by addressing unstable operating conditions.
- Monitor metal temperature: Ensure stable metal temperatures by regulating the holding furnace and operating conditions.
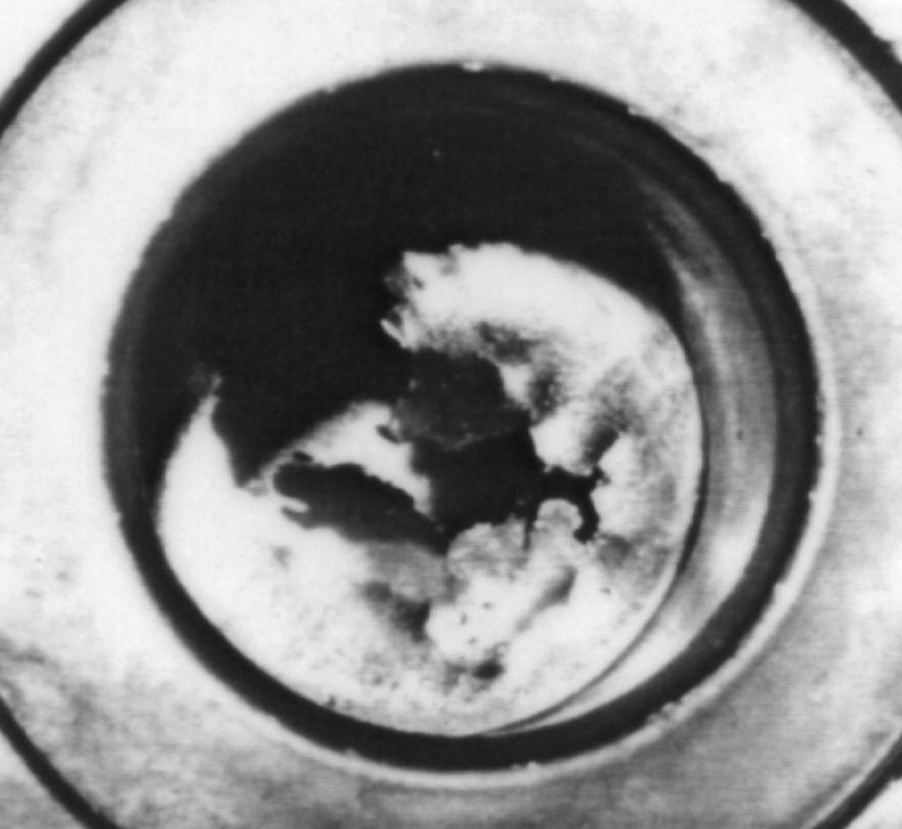
Example of excessive cast material
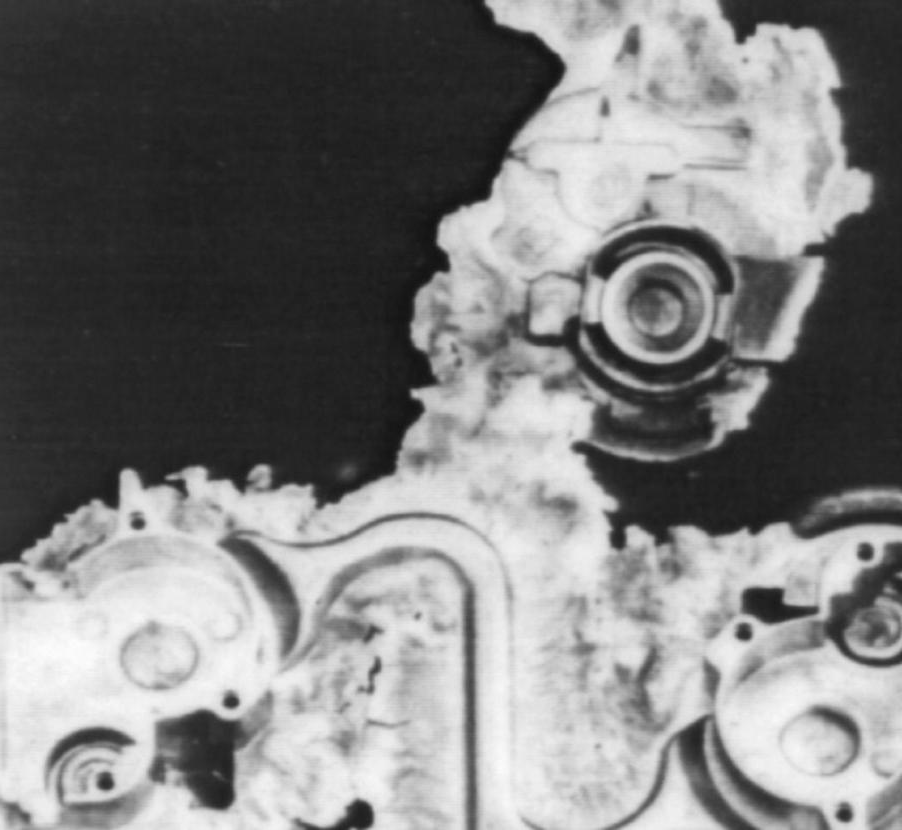
Example of very severe flash.
Please note that the information provided in this article is intended to be a general guide to the causes and corrections of flash in metal castings. However, it is important to note that the specific cause and correction of any particular defect will vary depending on the specific casting process, alloy, and other factors. Therefore, it is important to consult with an experienced and professional engineer to ensure that the correct diagnosis is made and the most suitable correction is chosen.