Solder Defect
Defects
Cause
Aluminum or magnesium can combine with die steel, causing cast metal to stick to the die surface. In zinc, the zinc forms a layer on top of the steel.
Corrections
- Aluminum:
- Reduce the temperature in the solder area, if possible. This is the best solution.
- Add a fountain (bubbler) in the solder area. Even a small fountain can be effective.
- Use a high heat transfer material in the solder area, such as TZM, ANVILLOY, or MITECH.
- Make sure the water lines are functioning and clean.
- Increase the spray on the solder area.
- Reduce the speed and increase the cycle time.
- Reduce the fill time.
- Reduce the length of time the metal impacts on the solder area.
- Check the metal velocity. Is it too high? The velocity should be above atomization but not much higher (about 1000 to 1400 ips).
- Check the PQ2 settings to find the best plunger size, speed, pressure, etc.
- Verify that the actual plunger size and speed are meeting the desired conditions.
- Check the draft angle at the solder point.
- Check for undercuts or a rough surface on the die at the solder point.
- Check the iron content of the alloy. If it is above 0.75%, use lower pressure if possible.
- Zinc (build-up):
- Lower the die temperature, if possible. This is the best action.
- Improve the die surface finish by reducing the surface roughness.
- Increase the draft angle.
- Apply a coating with a smooth surface, such as tin or crc.
- Polish the die using an inhibited acid to keep die damage to a minimum. Use 600 grit sandpaper.
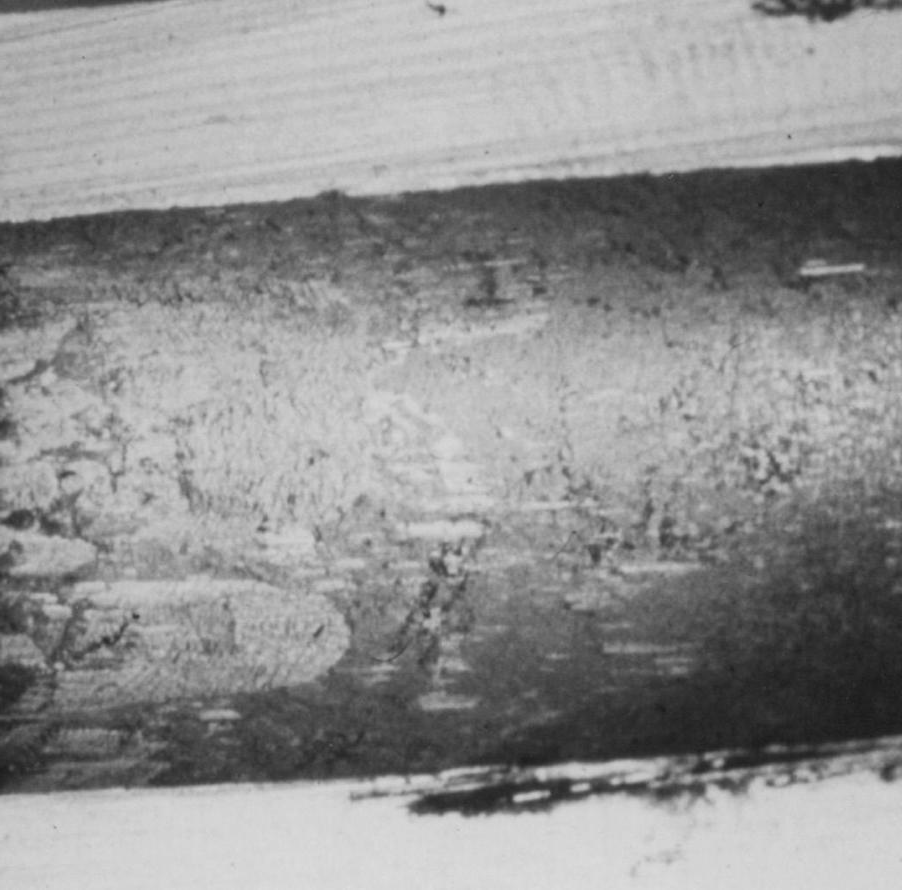
Please note that the information provided in this article is intended to be a general guide to the causes and corrections of solder defects in metal castings. However, it is important to note that the specific cause and correction of any particular defect will vary depending on the specific casting process, alloy, and other factors. Therefore, it is important to consult with an experienced and professional engineer to ensure that the correct diagnosis is made and the most suitable correction is chosen.