Surface Defects
Defects
- Cold flow: molten metal flows too slowly and cools before filling the mold
- Cold lap: two streams of molten metal meet and do not fuse together, creating a seam on the surface of the casting
- Chill: area of the casting that solidifies too quickly, resulting in a hard, brittle surface
- Non-fill: mold cavity is not completely filled with molten metal
- Swirls: marks on the surface of the casting caused by turbulent flow of molten metal
Cause
The leading edge of the metal flow is too cold and laps together.
Corrections
- Increase the die temperature, especially at the problem location. Check for the following causes of cold dies:
- Slow cycle time
- Excessive coolant flow
- Excessive spray
- Lack of overflows
- Reduce the fill time. This may require:
- Increasing the plunger speed
- Increasing the plunger size
- Increasing the gate area
- Increasing the hydraulic pressure
- Change the flow pattern (gating) by:
- Directing the flow at the problem area by moving the gate
- Changing the gate design to direct the flow in a different direction
- Changing the gate velocity
- Adding overflows to capture cold metal
- Check for low metal temperature by looking for:
- Delays that cool the metal
- Furnace temperature variations
- Low temperature swings
- Check for low pressure at the end of the shot by looking for:
- Dragging tips
- Poor sleeve condition
- Too little or inconsistent sleeve lubrication
- White buildup in the shot sleeve
- Check the accumulator pre-charge pressure.
- Check for a thin biscuit.
- Check for heavy flashing.
- Check for bubbling and turbulence in the hot chamber, which may be caused by bad rings or a poor gooseneck.
- Check the following:
- For aluminum alloys:
- Use the highest possible silicon content.
- Ensure that the metal is clean.
- For zinc alloys
- Use the highest possible aluminum content.
- Ensure that the other constituents are within range.
- Vents: ensure that they are open and sized correctly.
- Vacuum working: ensure that the vacuum is working properly.
- Thin wall sections:
- Check the minimum wall thickness for the fill time and temperatures being used.
- Look for design errors, such as designers not being aware of casting problems.
- Look for tool making errors, such as dimensions not being as expected.
- Look for uneven wall sections.
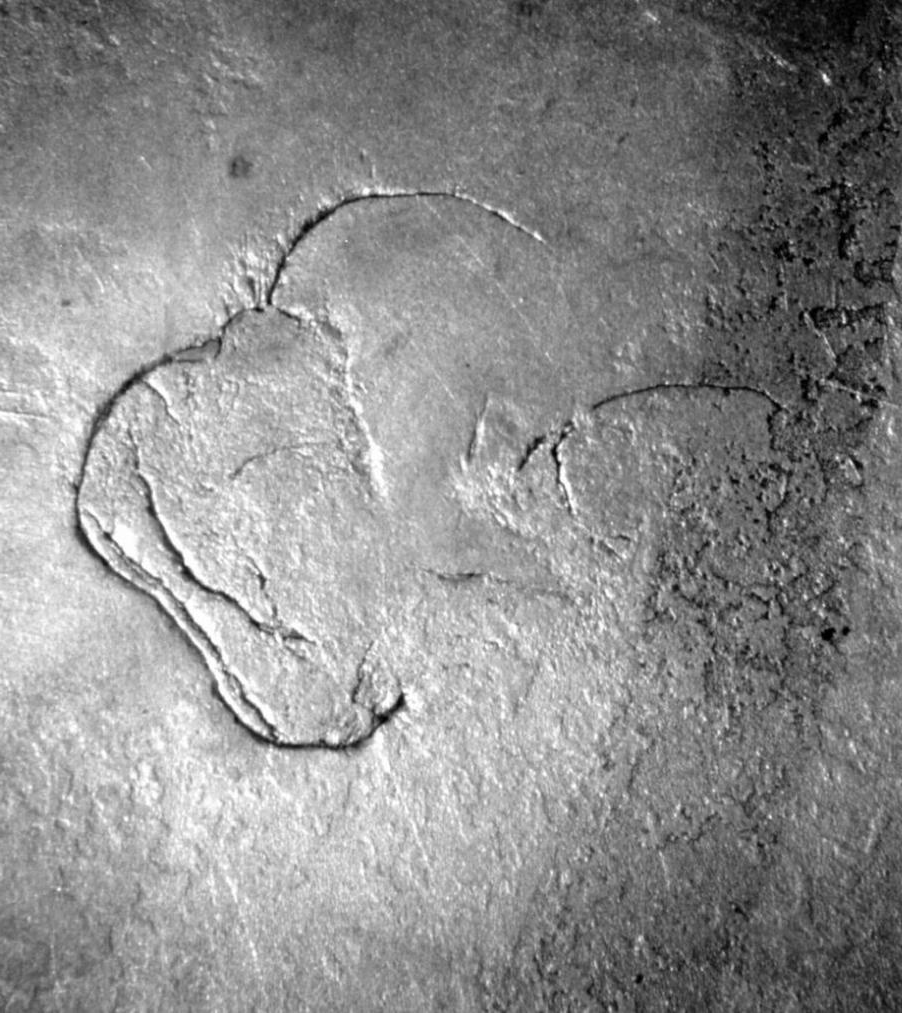
Typical surface defect (cold flow)
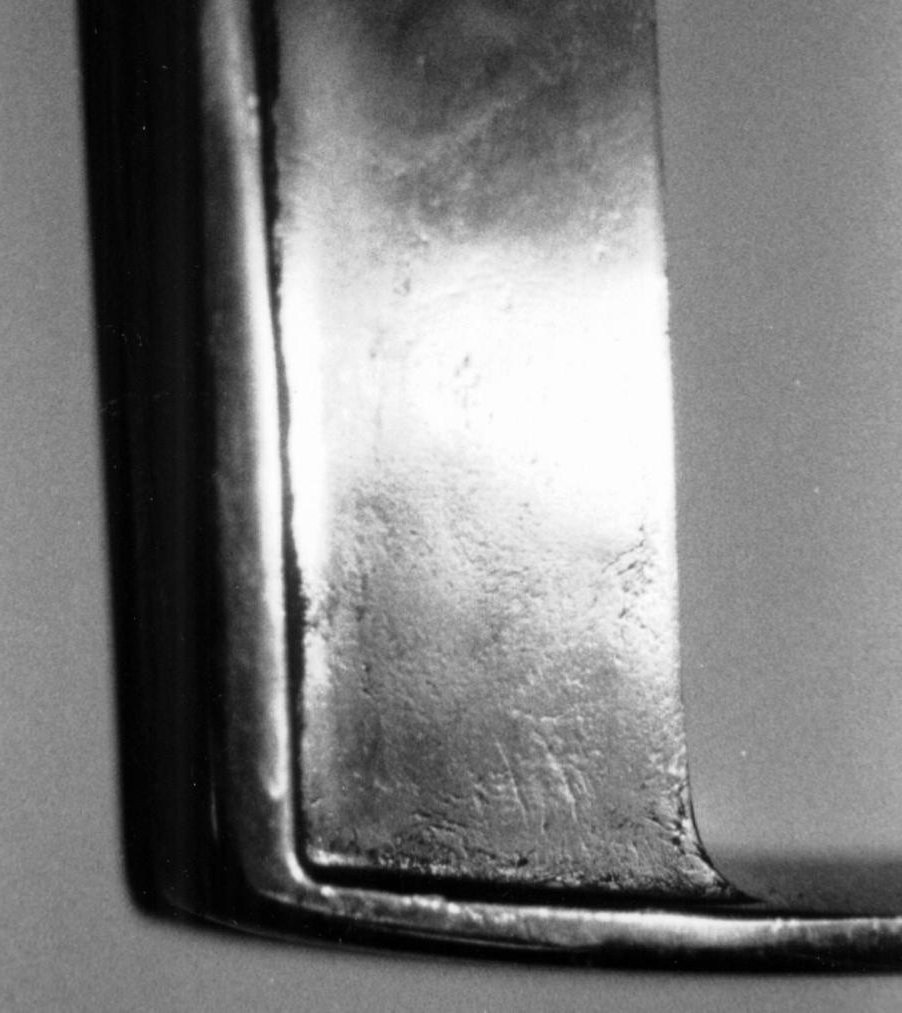
Typical surface defect (cold flow)
Please note that the information provided in this article is intended to be a general guide to the causes and corrections of surface defects in metal castings. However, it is important to note that the specific cause and correction of any particular defect will vary depending on the specific casting process, alloy, and other factors. Therefore, it is important to consult with an experienced and professional engineer to ensure that the correct diagnosis is made and the most suitable correction is chosen.