Gas Porosity Defect
Defects
Bubbles of gas trapped in the metal during die filling.
Cause
Gas trapped in the metal flow during die fill.
Corrections
- Eliminate trapped air:
- Use consistent pour rates.
- Delay after pouring to minimize splashing in the shot sleeve.
- Accelerate to slow shot speed correctly.
- Use critical slow shot speed.
- Accelerate to fast shot speed as late as possible.
- Check the runner for smooth flow:
- No sharp corners.
- No blind ends or pockets.
- Ever decreasing areas properly used in runner path.
- Check the vents:
- Right size (big enough).
- Vents kept open (not full of flash).
- Located at the last point to fill.
- Vents go to the edge of the die.
- Check the vacuum system:
- Vacuum channels big enough.
- Vacuum channels located at last point to fill.
- Filters cleaned and open.
- Vacuum valves working.
- Vacuum level adequate.
- Eliminate gas from lubricant:
- Use the minimum possible amount of plunger lubricant.
- Avoid putting lubricant in front of the tip.
- Use consistent application procedures.
- Avoid excessive die lubricant or anti-solder paste.
- Eliminate steam:
- Make sure the die is dry when it closes.
- Use lots of air blow-off.
- Put drain holes in die where die lube (water) could accumulate.
- Check for water leaks after die is locked.
- Check for leaks from sprayer, hydraulic cylinders, etc.
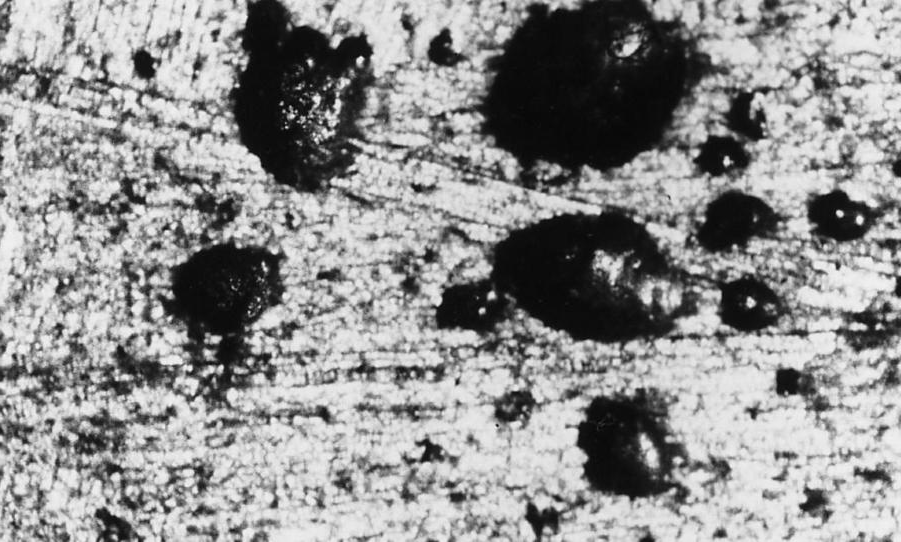
Some typical trapped gas porosity, showing the shiny walls, as well as, shinny walls and a wall that is sometimes smooth and sometimes rough, due to oxide (10X).
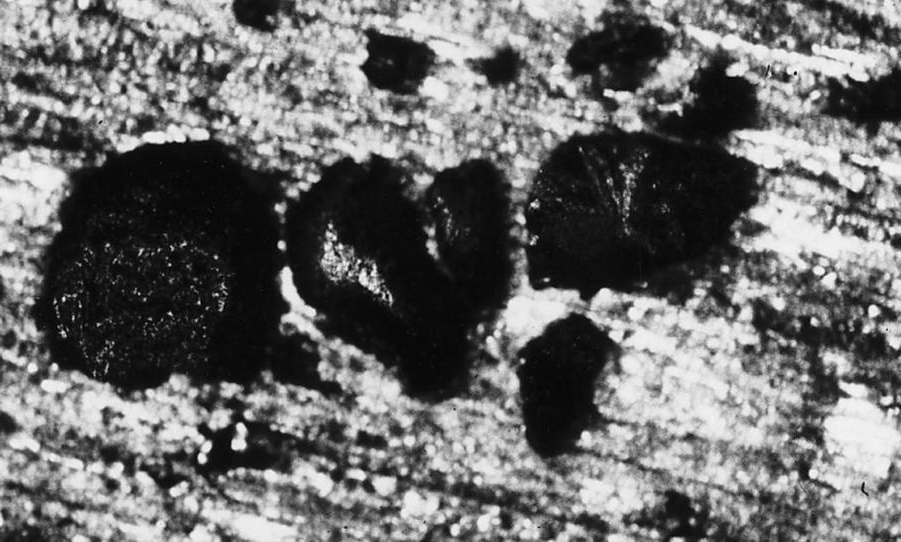
More trapped gas with a typical grouping of non-connected bubbles, and some probable dross inclusions at the bottom of one bubble (10X).
Please note that the information provided in this article is intended to be a general guide to the causes and corrections of gas porosity in metal castings. However, it is important to note that the specific cause and correction of any particular defect will vary depending on the specific casting process, alloy, and other factors. Therefore, it is important to consult with an experienced and professional engineer to ensure that the correct diagnosis is made and the most suitable correction is chosen.