Flow Porosity Defect
Defects
Flow porosity
Cause
Metal flow is too slow, too cold, or has a poor flow pattern, leaving spaces (porosity) between solidified metal flows.
Corrections
- This is a metal flow problem, so the same corrections apply as those listed for surface defects.
- The spaces between metal flows may appear on the surface (hole) or inside (porosity).
- The biggest factor is the fill time. Calculate and measure the fill time to make sure it is fast enough. If in doubt, reduce the fill time as much as possible.
- Stabilize furnace operation (reduce variation to a maximum of +/- 6°C) and use the correct metal temperature.
- Metal temperature at the gate is important. In aluminum, watch for heat loss in the ladle and shot sleeve. Add more superheat to compensate for this heat loss.
- Stabilize die temperature and run at a higher die temperature (>205°C).
- Review and correct metal pressures:
- Review the static metal pressure. It should be above 2000 psi for zinc and 3000 psi for aluminum and magnesium.
- Check intensifier operation.
- Consistency is most important.
- The pressure must rise quickly enough. Measure and evaluate the rise time. The best time will vary depending on the casting shape.
- The pressure setting must be high enough. A final pressure of >6000 psi is acceptable, but >9000 psi is best.
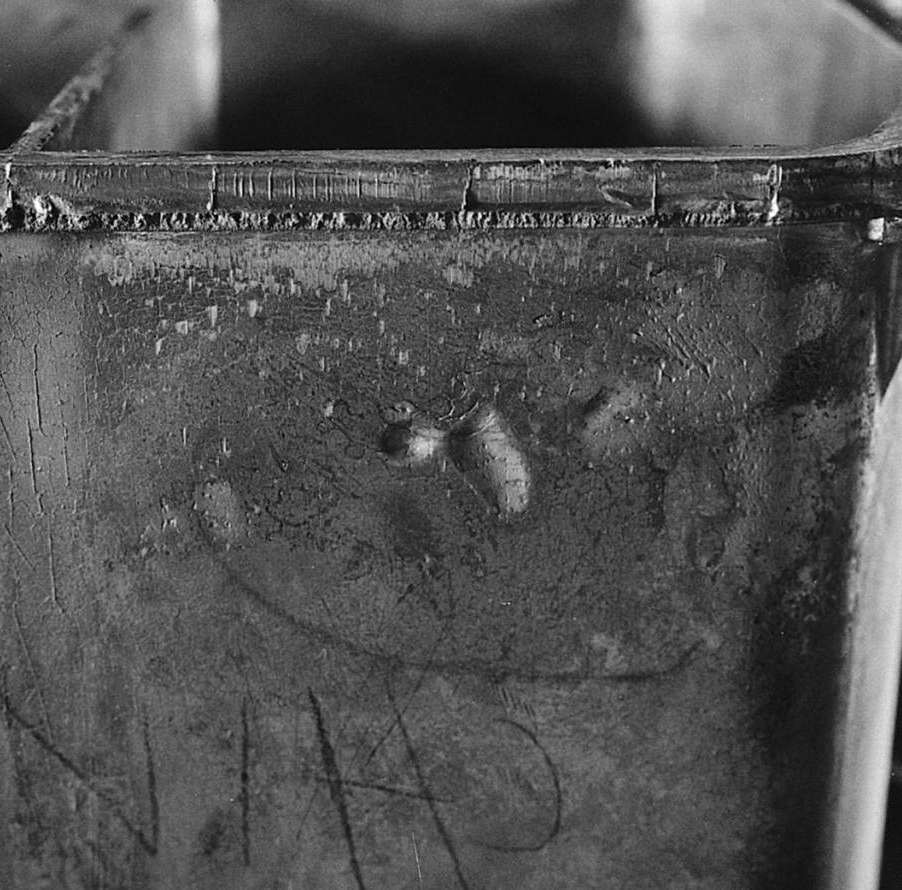
Surface from poor flow – caused by stuck plunger once every 10 shots or so.
Please note that the information provided in this article is intended to be a general guide to the causes and corrections of flow porosity in metal castings. However, it is important to note that the specific cause and correction of any particular defect will vary depending on the specific casting process, alloy, and other factors. Therefore, it is important to consult with an experienced and professional engineer to ensure that the correct diagnosis is made and the most suitable correction is chosen.