Cracks and Tears Defect
Defects
Cause
Many causes, including shrinkage cracks on the surface, casting being stretched in the die, mechanical stress at die opening, ejection, or from trimming.
Corrections
- Examine the casting to determine the most probable cause.
- If shrinkage cracks are the problem:
- Check for good radii at the crack location.
- Cool the hot spot.
- Heat up the adjacent cool spots.
- Add pressure in this area during solidification.
- If stress cracks during cooling and after solidifying are the problem:
- Reduce stress risers (add radius as much as possible).
- Shorten the hold time.
- Look for thin wall castings that cool before the runner; in this case, cool the runner and eject sooner.
- Add wall thickness if possible.
- If the biscuit determines the hold time, then add cooling to the biscuit.
- Change the runner shape if necessary to eject sooner.
- If mechanical forces or die shift during die opening are the problem:
- Watch as the dies separate, look for evidence of die shift (ejector die drops forward as the dies separate).
- Watch as the dies close; if the die guide pins carry the load, it is likely that there is stress on the casting during opening.
- Add a die carrier under the ejector die.
- Reset the die to re-align the ejector half better.
- Adjust the shoes under the moveable platen as needed.
- Check the tie bar stress for even locking.
- Check the condition of the linkage; repair as necessary.
- Check the condition of the tie bar bushings; repair as necessary.
- If ejection is the problem:
- Check that the ejection movement is straight, guided, and does not wobble during ejection.
- Check for drags, lack of draft, or undercuts.
- Eject slower and smoother.
- Check the slides for proper action (slides are not worn out and wobbly).
- Check the metal constituents:
- In aluminum, check the proportion of Fe, Cu, and Si; also check for the presence of silicon modifiers.
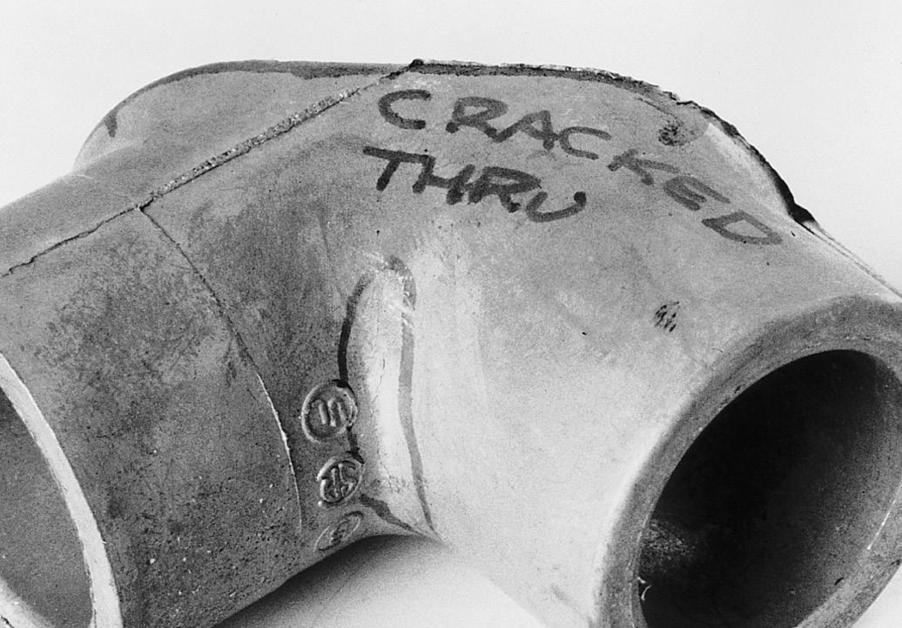
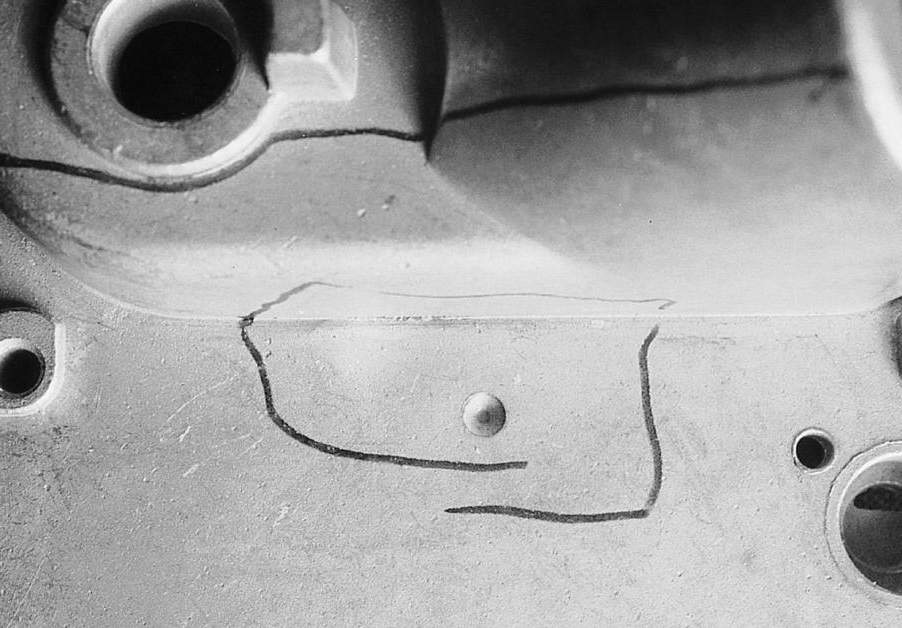
Please note that the information provided in this article is intended to be a general guide to the causes and corrections of cracks and tears defects in metal castings. However, it is important to note that the specific cause and correction of any particular defect will vary depending on the specific casting process, alloy, and other factors. Therefore, it is important to consult with an experienced and professional engineer to ensure that the correct diagnosis is made and the most suitable correction is chosen.