Outgassing Defect
Defects
Cause
Bubbles appear on the casting surface during a painting or finishing operation. This is caused by a leak path that develops through the casting skin when the casting is heated during finishing, allowing the heated and expanding trapped gas to escape.
Corrections
- If the problem is in the overflow gates, minimize or combine the number of overflow gates used, or reduce their size.
- Keep the overflow gates away from the edge of the castings to minimize heat buildup next to the casting.
- Make the main gate thinner while still maintaining the appropriate gate area for casting quality needs.
- Reduce the metal temperature, but stay above 420°C for zinc and above about 650°C for aluminum.
- Reduce the die temperature at the gate.
- Reduce trapped gas by using a slow shot speed on the plunger (hot chamber) and reducing spray to the absolute minimum.
- Make sure there is pressure at the end of the stroke by checking for the following:
- No thin biscuits or leaking plunger rings
- Proper metal pressure, both static pressure and intensified (right size plunger)
- Correct accumulator pre-charge
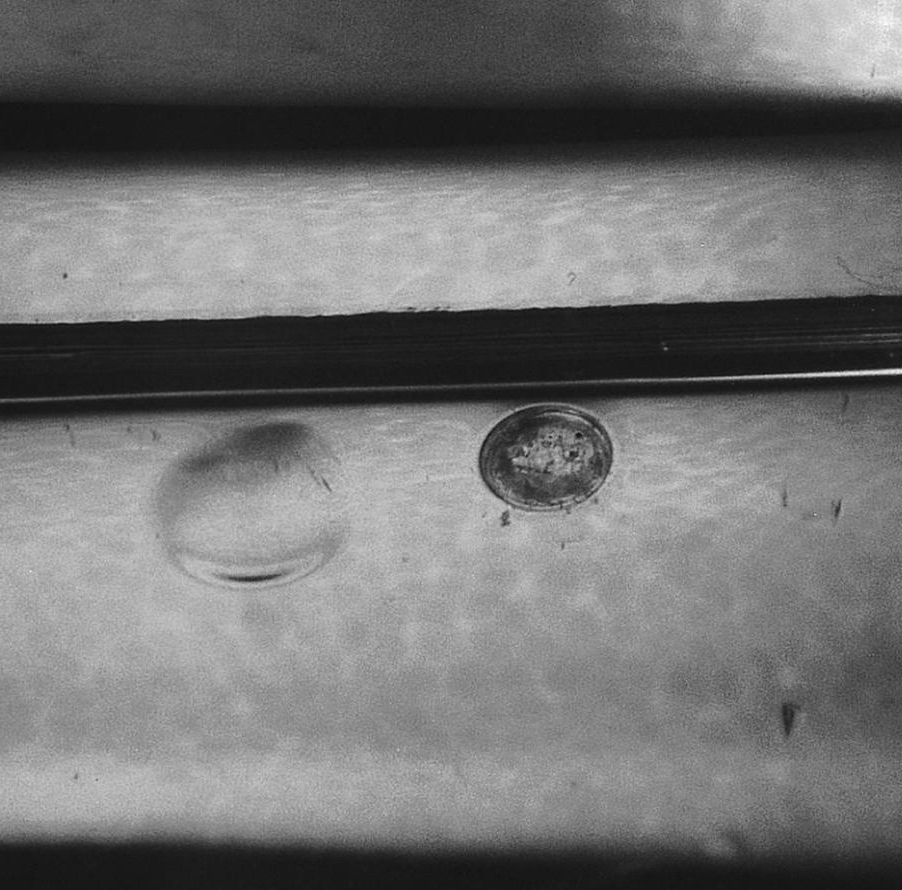
Please note that the information provided in this article is intended to be a general guide to the causes and corrections of outgassing defects in metal castings. However, it is important to note that the specific cause and correction of any particular defect will vary depending on the specific casting process, alloy, and other factors. Therefore, it is important to consult with an experienced and professional engineer to ensure that the correct diagnosis is made and the most suitable correction is chosen.