Excessive Flux Defect
Defects
Cause
Excessively applied flux can lead to increased porosity and surface corrosion. This can be identified by submerging the casting in clean water overnight and observing for white spots in areas with porosity, or by examining a fracture through the porous area.
Corrections
-
Review and refine flux usage procedures: Collaborate with experts to determine the optimal amount of flux required for effective casting processes and establish proper application techniques.
-
Document flux usage procedures: Clearly document the revised flux usage procedures, including the recommended quantity of flux and the appropriate application methods.
-
Provide comprehensive training to operators: Thoroughly train operators on the correct amount of flux to use and the proper application techniques to ensure consistent and controlled flux usage.
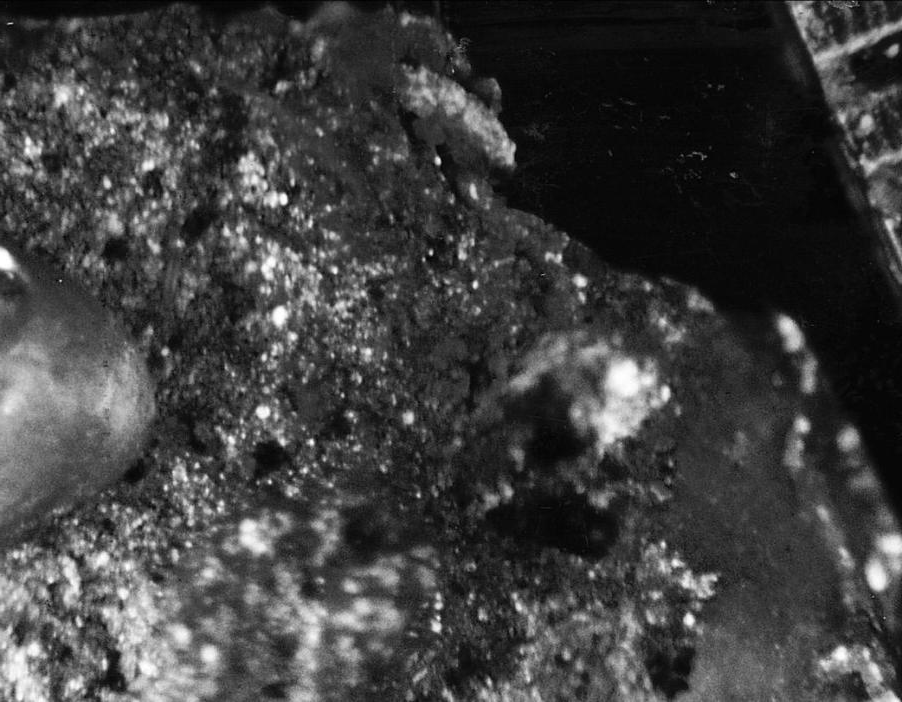
Please note that the information provided in this article is intended to be a general guide to the causes and corrections of excessive flux in metal castings. However, it is important to note that the specific cause and correction of any particular defect will vary depending on the specific casting process, alloy, and other factors. Therefore, it is important to consult with an experienced and professional engineer to ensure that the correct diagnosis is made and the most suitable correction is chosen.