Aluminum Extrusion Die Design Considerations
Aluminum extrusion plays a critical role in modern manufacturing, especially in industries requiring precise and intricate profiles, such as automotive, aerospace, and construction. The quality of an aluminum extruded product is significantly influenced by the design of the extrusion die, which determines factors like dimensional accuracy, surface finish, and mechanical properties.
This article explores the in-depth considerations necessary for designing aluminum extrusion dies that meet both industry standards and customer expectations.
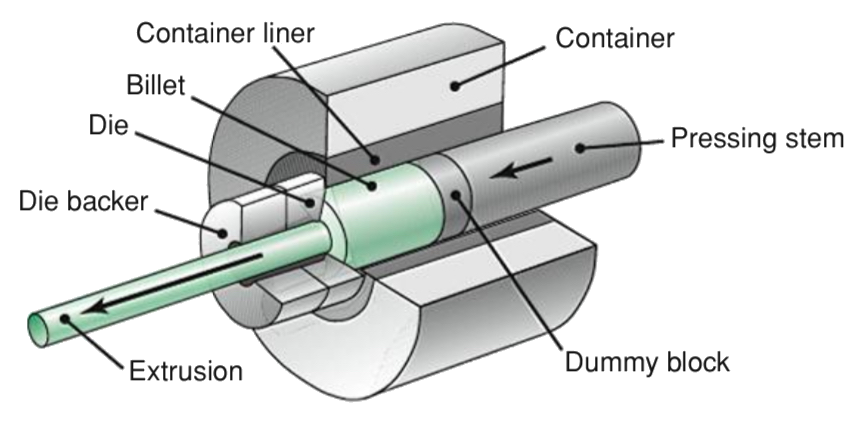
Schematic illustration of the direct-extrusion process.
- Material Selection Die materials are selected based on their ability to withstand the high temperatures and pressures inherent in the extrusion process. Hot-work tool steels, such as H13, are the industry standard due to their excellent thermal fatigue resistance, toughness, and wear resistance. Coatings, such as nitriding or chrome plating, can further enhance durability by reducing surface wear and oxidation. Advanced materials and coatings help extend die life, minimize maintenance costs, and improve extrusion efficiency.
- Die Geometry and Flow Balance Die geometry is crucial for directing material flow uniformly through the die opening. A well-designed geometry can prevent common extrusion defects, such as:
- Surface tearing: Occurs due to uneven material flow.
- Wall thickness variation: Caused by imbalanced die design, impacting product integrity.
- Bearing Length and Profile Control The bearing length—the portion of the die that shapes the final profile—is fundamental in controlling dimensions and ensuring a smooth finish. Proper bearing length is especially critical for complex profiles and hollow sections, as it maintains uniformity across the cross-section. Precision here ensures that the extruded profile meets strict tolerances, reducing rework and material wastage.
- Cooling Systems and Thermal Management Thermal management is a key factor in aluminum extrusion, as excessive heat can lead to die deformation and product defects. Cooling channels within the die regulate temperature, preventing unwanted thermal expansion. Controlled cooling also minimizes residual stresses, which can impact mechanical properties and lead to warping.
- Die size and shape.
- Extrusion speed.
- Required finish and tolerance.
- Lubrication: Enhancing Die Performance and Lifespan Lubrication reduces friction between the billet and die, ensuring smoother material flow, reducing wear, and extending die life. Specialized lubricants are used in aluminum extrusion to balance slip and adhesion at critical contact points. Proper lubrication lowers the extrusion force required, thereby reducing energy costs and improving die performance.
- Support Mechanisms and Die Alignment Proper die alignment is essential to prevent deflection and ensure precise profile dimensions. In multi-hole dies used for high-output extrusions, support mechanisms are even more critical, as even minor miss-alignments can lead to substantial variations in profile quality. Robust support and alignment prevent deformation and ensure uniform material flow, reducing production errors and scrap rates.
- Stress Analysis for Enhanced Die Durability Stress analysis is a critical step in extrusion die design, enabling designers to identify stress concentrations and potential failure points. Finite Element Analysis (FEA) can simulate operational stresses, including thermal loads and mechanical forces, to optimize die structure and materials. Through FEA, designers can adjust die geometry to distribute stress evenly, enhancing both die life and product consistency.
- Advances in Die Design for Aluminum Extrusion Recent advancements in die design and manufacturing technology have expanded the possibilities for aluminum extrusion. Technologies such as 3D printing and computer-aided manufacturing (CAM) allow for faster prototyping, testing, and refinement of dies. These advancements help companies stay competitive by reducing lead times, lowering costs, and enabling rapid adjustments to meet changing customer demands.
For complex profiles, variable bearing lengths can be employed, where thicker sections have longer bearing lengths to compensate for flow disparities.
The cooling system design must be optimized for each specific extrusion profile, considering factors like:
Alignment aids include hydraulic or mechanical clamping systems that stabilize the die position during extrusion.
Stress analysis also guides the design of reinforcement ribs or inserts for larger or more complex dies, ensuring they can withstand high-volume production without compromising quality.
Moreover, with the integration of machine learning in die design, manufacturers can predict and correct extrusion issues before production, saving valuable resources.
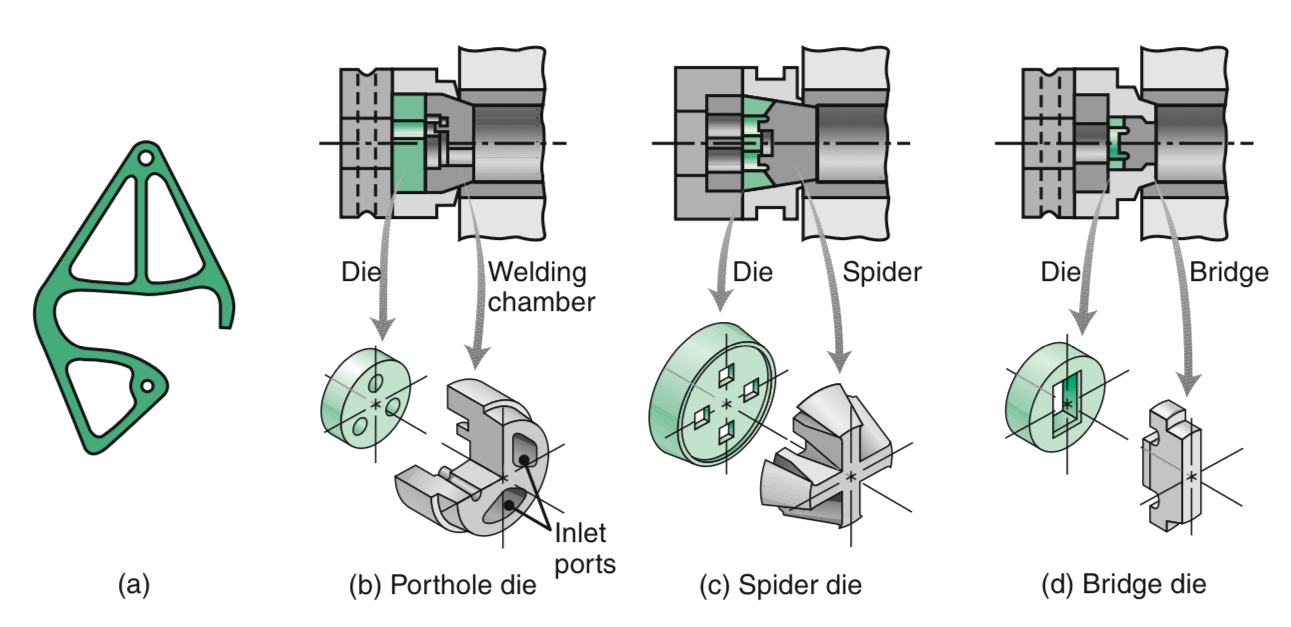
(a) An extruded 6063-T6 aluminum-ladder lock for aluminum extension ladders. (b) through (d) Components of various dies for extruding intricate hollow shapes.
Conclusion
Effective aluminum extrusion die design is essential for producing high-quality, precision profiles efficiently. By carefully considering each aspect—material selection, die geometry, bearing length, cooling and lubrication, support, alignment, and stress analysis—manufacturers can optimize the extrusion process, minimize defects, and extend die lifespan.The aluminum extrusion industry is continuously evolving, with new materials, techniques, and technologies allowing for more complex profiles and enhanced material properties. Staying abreast of these innovations is vital for companies aiming to deliver the highest standards in extruded aluminum products.