Heat Treatment: Concept and Methods
Heat treatment in metallurgy involves controlled heating and cooling to alter steel properties, achieving desired characteristics such as strength, hardness and ductility.
Annealing
Heating steel above its critical point and then slowly cooling it reduces hardness, improves machinability and relieves internal stresses, resulting in a uniform microstructure.
Normalizing
Heating steel above its critical point and cooling in air refines grain structure, enhances mechanical properties and eliminates residual stresses.
Hardening
Heating steel above the critical point followed by rapid cooling (quenching) in water, oil or air transforms its structure, producing a harder phase called martensite.
Tempering
Reheating hardened steel to a temperature below its critical point and controlled cooling reduces brittleness while maintaining hardness. Properties depend on tempering temperature and time.
Quenching and Tempering
Combining hardening and tempering achieves desired toughness and ductility by first hardening and then tempering the steel.
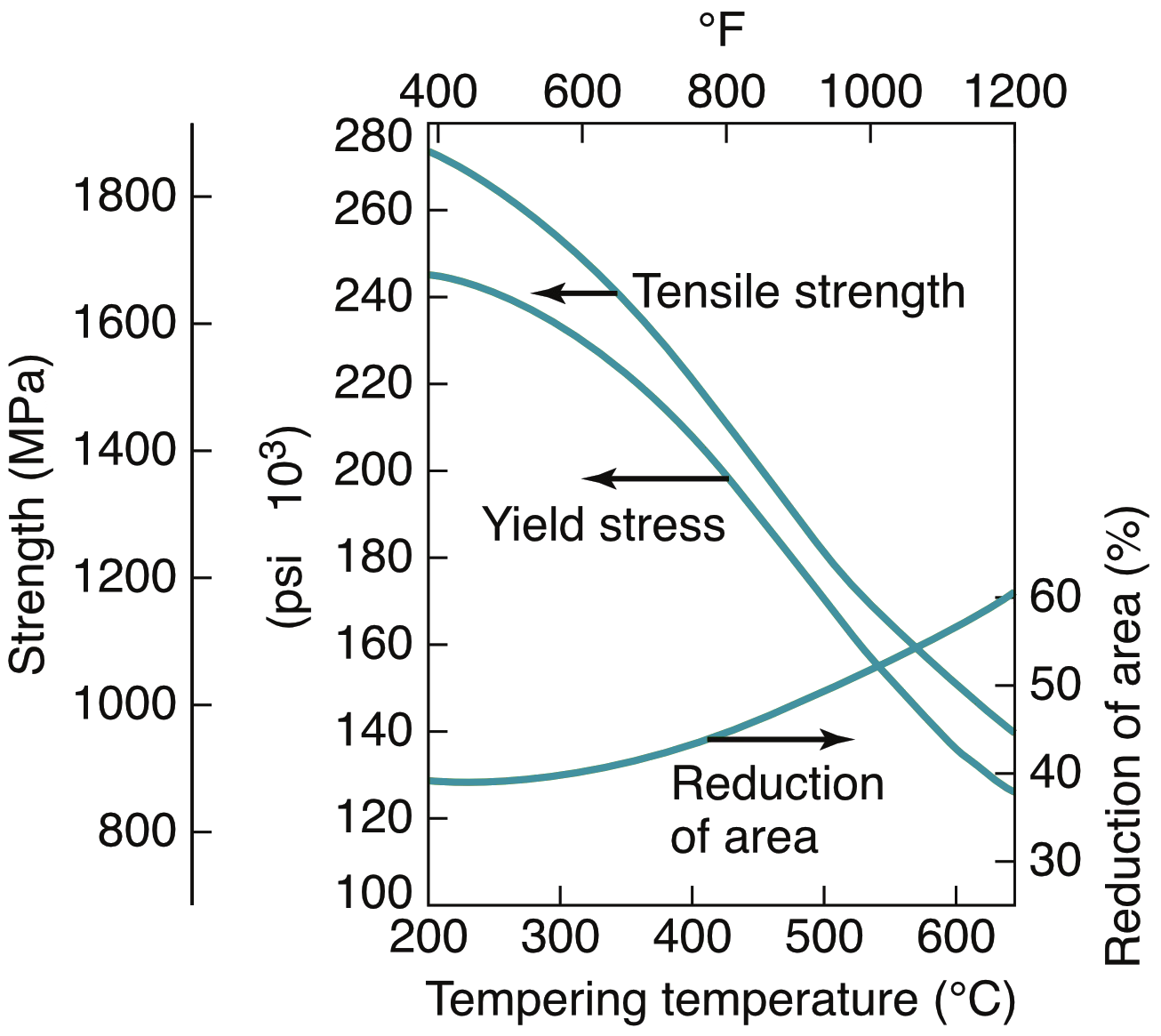
Case Hardening
Hardening only the surface of steel while keeping the core soft and tough is crucial for components requiring surface wear resistance and core toughness. Techniques include carburizing, nitriding, carbonitriding and induction hardening.
Austempering and Martempering
Both are isothermal heat treatment. Austempering quenches steel above the martensite start temperature, holding until bainite transformation is complete. Martempering quenches just above the martensite temperature, followed by cooling to produce uniformly hardened steel or reduce distortions and residual stresses.
The choice of heat treatment method depends on the desired combination of hardness, toughness, and ductility, as well as the specific type of steel being treated. Each method offers unique advantages tailored to meet diverse industrial requirements.
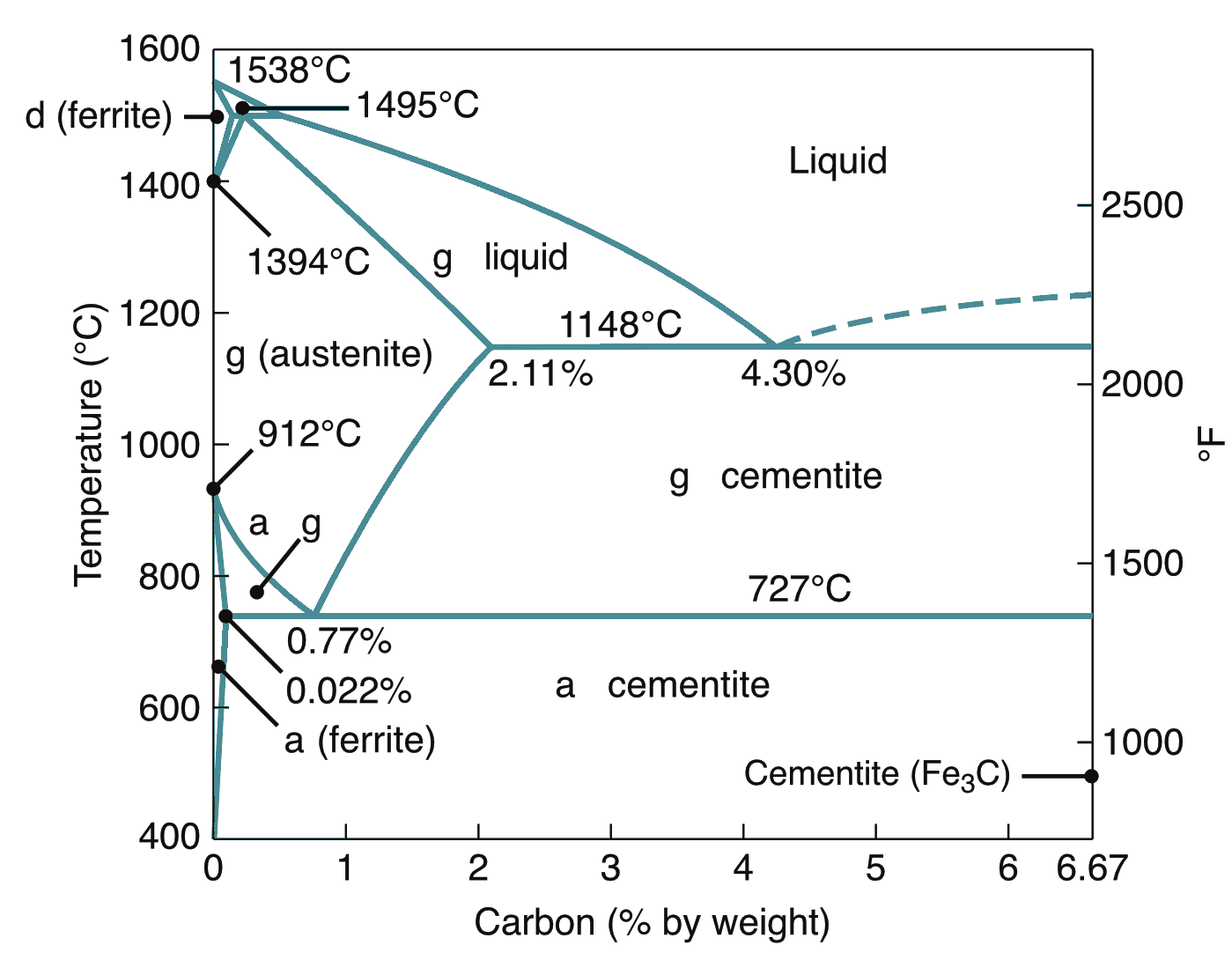