Exploring the Plastic Injection Molding Process & Types
Plastic injection molding is a versatile, efficient, and widely used method in the manufacturing sector for producing large volumes of identical plastic parts. It involves injecting molten plastic into a mold and then allowing it to cool and solidify into the desired shape. The process is used extensively in various industries, including automotive, medical, electronics, and consumer goods, due to its ability to produce high-quality parts with high precision and repeatability.
The Plastic Injection Molding Process
The plastic injection molding process consists of a series of stages:
- Material Preparation: The plastic pellets are first fed into the injection molding machine's hopper. The machine then heats the plastic until it reaches a molten state.
- Injection: The molten plastic is forced into the mold cavity using a reciprocating screw or a ram injector. The pressure exerted ensures the plastic fills and conforms to every part of the mold.
- Cooling and Solidification: Once the mold is filled, the plastic is allowed to cool and solidify, forming the desired part. The cooling time depends on the plastic's type, thickness, and the mold's design.
- Ejection: After the plastic solidifies, the mold opens, and the part is ejected. The process then repeats for the next cycle.
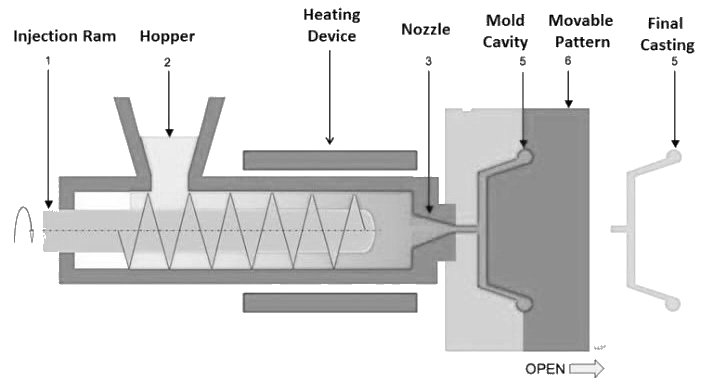
Plastic Injection Molds and Their Types
The quality of the produced part largely depends on the mold used in the injection molding process. The mold, typically made from steel or aluminum, consists of two halves—the injection mold (cavity) and the ejector mold (core). Here are some of the commonly used plastic injection mold types:
- Single-Cavity and Multi-Cavity Molds: Single-cavity molds produce one component per injection cycle, while multi-cavity molds produce multiple identical parts per cycle, increasing production efficiency. However, multi-cavity molds require a more precise alignment and are therefore more expensive.
- Family Molds: These molds produce several different parts of a single product in one cycle. They are cost-effective when small quantities of multiple related parts are needed, but they require precise control over each cavity's filling.
- Hot Runner Molds: Hot runner molds use a heated physical channel that guides molten plastic into the injection mold cavity, reducing plastic waste and cycle times. However, these molds are more complex and expensive than the standard cold runner molds.
- Two-Shot Injection Molds: Also known as dual-shot, 2K, or overmolding, this process involves injecting two different materials into the mold in consecutive steps. This method is used when parts require multiple materials or colors.
- Insert Molding: In this process, a preformed part—often metal—is placed into a mold, which is then filled with plastic. The result is a single piece with the insert encapsulated by the plastic. This process is used to create parts that combine the strength of metal with the flexibility and durability of plastic.
- Prototype/Testing Molds: These molds are used for prototyping and testing new product designs before mass production. They are typically made from less expensive materials, such as aluminum or 3D-printed molds, to reduce costs and allow for design modifications during the testing phase.
- Stack Molds: Stack molds consist of multiple mold parting surfaces stacked on top of each other, allowing for simultaneous production of multiple parts in each cycle. They are commonly used for high-volume production and can significantly increase productivity.
- Unscrewing Molds: Unscrewing molds are used when a part has internal or external threads that need to be formed during the injection molding process. These molds have rotating cores or threads that unscrew from the molded part after it solidifies, enabling the production of threaded plastic components.
- Collapsible Core Molds: Collapsible core molds are employed to produce complex parts with internal undercuts or holes. The mold has retractable cores that collapse during ejection, allowing the part to be released from the mold without the need for side actions or slides.
- Gas-Assisted Molds: Gas-assisted molding involves injecting pressurized gas into the mold cavity after plastic injection. This process creates hollow sections or helps improve part quality by reducing sink marks, warpage, and internal stresses.
Plastic injection molding molds are essential components in the plastic injection process, playing a crucial role in producing high-quality plastic parts efficiently. The selection of the appropriate mold type depends on factors such as the part's design, complexity, volume requirements, and cost considerations. By understanding the various mold types and their unique capabilities, manufacturers can make informed decisions to optimize the injection molding process, improve productivity, and achieve superior product quality.