Optimizing Die Design: Key Considerations for Precision Sheet Metal Forming
When designing a die for a punching or forming operation, various critical factors must be considered. The choice of material for the die is crucial, with considerations extending beyond the sheet metal to include properties like heat resistance, wear resistance, and toughness. These properties ensure the die withstands repeated operations without degradation. Additionally, the complexity of the final product influences die design, often requiring advanced features such as multiple stages, forming inserts, or specialized coatings to achieve precision.
The thickness of the sheet metal is another essential consideration. Thicker materials demand more force, necessitating stronger or more durable dies. The thermal impact of the punching or forming process should also be managed, incorporating features like cooling channels in the die design or utilizing materials with superior heat dissipation properties.
Die Maintenance
Maintaining dies in optimal condition is crucial for efficient and quality operations. Regular inspection and cleaning prevent material build-up on the die and detect signs of wear or damage. Lubrication plays a pivotal role in die maintenance, reducing friction during operations and extending the die’s lifespan. The surface finish of the die is equally important, influencing the quality of the formed product. Coatings such as nitriding or those with low friction coefficients enhance the die’s durability and performance.
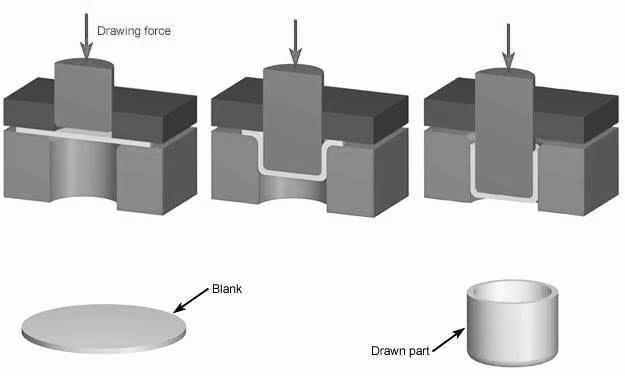
Die Setting
Die setting, the process of correctly positioning the die in the press, is critical for achieving accurate results and preventing damage to the die or press. Proper die setting involves aligning the die with the punch, adjusting the press stroke, and setting the correct pressure for the operation. Die clearance, a vital aspect of this process, determines the balance between shearing force and wear on the punch and die.
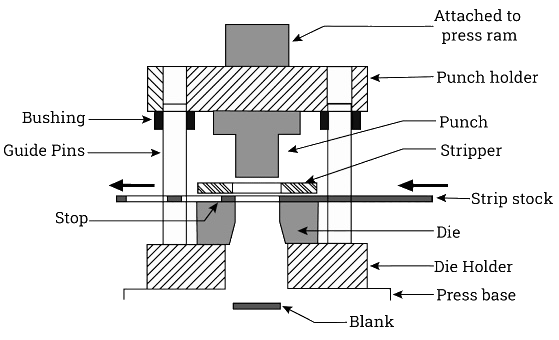
Punch Die Clearance Optimization
Optimal punch die clearance is paramount for successful punching or forming operations. It influences material deformation, with too little clearance resulting in burrs and excessive distortion, while excessive clearance can lead to imprecise cuts or uneven forming. The correlation between material thickness and punch die clearance is crucial, with thicker materials requiring larger clearances for increased deformation and vice versa for thinner materials.
Punch die clearance also affects tolerance and surface finish. Consistent clearance settings contribute to achieving tight tolerances and a smoother surface finish, minimizing the need for additional finishing processes. Temperature fluctuations during the punching process must be considered, as they can impact material behavior and clearance requirements. Regular maintenance is essential to address wear on the punch and die, which can alter clearance settings over time.
Adjustability in die design is key, allowing for fine-tuning based on material variations, tool wear, or specific project requirements. This flexibility ensures optimal performance in diverse production scenarios.
Sheet metal punching and forming processes are fundamental in manufacturing, facilitated by dies that serve as the backbone of operations. By understanding the intricate details of die design, maintenance, and punch die clearance optimization, manufacturers can optimize processes, improving efficiency and product quality. Emerging technologies, such as real-time monitoring and adaptive die control systems, further contribute to the evolution of these essential manufacturing processes.