Climb Milling vs Conventional Milling: A Comparative Analysis and Application Recommendations
The milling process, a key element of manufacturing, utilizes a revolving cutting tool to remove material from a workpiece. The two main categories of milling are climb and conventional, each exhibiting unique advantages and drawbacks. Recognizing the nuances between climb milling and conventional milling can assist manufacturers in achieving superior surface finishes, managing cutting forces effectively, and retaining dimensional precision.
Climb Milling
Climb milling operates such that the cutter spins in the same direction as the feed. This means that the cutting tool begins interaction with the workpiece material at the cut's commencement and moves in alignment with the workpiece's feed direction. This approach is also known as down milling due to the downward trajectory of the cutter's motion.
Force Impact: In climb milling, the cutting force is directed downwards, helping to anchor the workpiece against the machine table. This downward force decreases the likelihood of the workpiece lifting, thereby reducing tool wear and potential damage.
Surface Finish: Climb milling typically yields a superior surface finish. Since the cutter initiates cutting the workpiece with a minimal contact area, there is a reduced chance of recutting chips.
Dimensional Accuracy: While climb milling can offer greater accuracy on certain machines, it necessitates a machine with robust backlash control. The direction of the cutting forces can potentially cause cutter movement, which could impact accuracy.
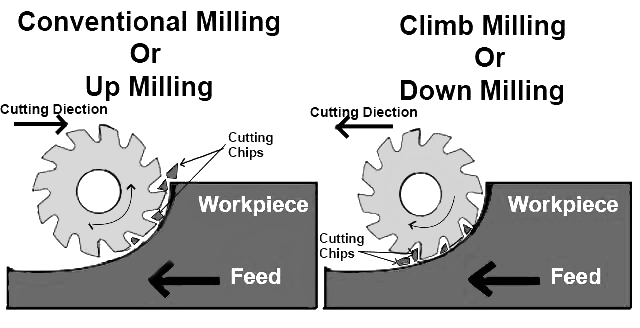
Conventional Milling
Conventional milling, also known as up milling, is a process where the cutter rotates counter to the direction of the feed. The cutting tool interacts with the workpiece material at the cut's end and cuts against the feed direction.
Force Impact: In conventional milling, the cutting forces act upward, potentially causing the workpiece to lift if not properly secured. This technique can increase tool wear and potential damage due to the upward force on the workpiece.
Surface Finish: Conventional milling often results in a lower quality surface finish compared to climb milling. This is due to the cutter interacting with a large contact area, increasing the likelihood of recutting chips.
Dimensional Accuracy: Conventional milling can deliver good dimensional precision, particularly on machines with significant backlash. The direction of the cutting force tends to keep the backlash out of the cut, thus reducing the potential for a dimensional error caused by backlash.
The choice between climb milling and conventional milling hinges on your specific needs and the capabilities of the machine. In general, climb milling offers a better surface finish and reduced tool wear but requires a machine with excellent backlash control to maintain dimensional accuracy. On the other hand, conventional milling may lead to increased tool wear and a lower quality surface finish, but it can deliver good dimensional precision, especially on machines with substantial backlash.
For roughing strategies, conventional milling is often recommended due to its effectiveness in chip evacuation and less demand on machine rigidity and backlash control. However, for finishing strategies where a superior surface finish and tighter dimensional accuracy are desired, climb milling is often the preferred choice given that the machine is capable of handling the backlash. By understanding these two milling techniques' differences, you can choose the most appropriate method for each specific application, ensuring optimal efficiency, productivity, and product quality.