The Aluminum Extrusion Process & Types
Aluminum extrusion is a versatile process used in industries like construction, automotive, and electronics. It involves heating an aluminum alloy billet to soften it, then pushing it through a die under high pressure to create a specific shape. Key types of aluminum extrusion dies include solid, hollow, semi-hollow, container, and seamless dies.
Solid Dies
Used for creating solid shapes like rods and beams, solid dies produce consistent profiles through direct extrusion methods. These dies are straightforward in design and are used for making parts without any internal cavities or voids.
Hollow Dies
Hollow dies create tubes or hollow products using mandrels supported by bridges to maintain the hollow structure during extrusion. These dies are more complex because they require additional components to form the internal cavities.
Semi-Hollow Dies
Semi-hollow dies produce profiles with partially enclosed voids, allowing for complex shapes with limited hollow spaces. These dies have a partially enclosed design which can create more intricate profiles compared to solid dies.
Container Dies
Container dies are utilized for complex hollow profiles. In this process, the billet is pushed into a container and extruded through the die at the end. This method helps in maintaining the integrity of the billet and achieving precise shapes.
Seamless Dies
Seamless dies produce seamless tubes by extruding aluminum into a hollow die and further treating it to eliminate seam lines, crucial for high-strength applications. This process involves additional steps to ensure the finished product has no seams or weld lines.
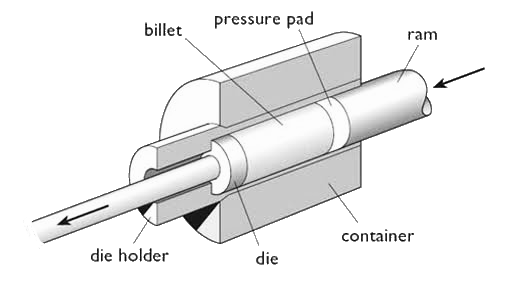
Extrusion Process Overview
Billet Preparation: The aluminum alloy billet is preheated to a specific temperature to make it malleable.
Extrusion: The billet is pushed through the die, shaping the aluminum into the desired profile.
Cooling: The extruded aluminum is cooled rapidly to retain its shape and properties.
Cutting: The extruded profiles are cut to the required lengths.
Finishing: The profiles undergo various finishing processes, including anodizing, painting, or powder coating, to enhance appearance and durability.
Advantages of Aluminum Extrusion
Versatility: Capable of producing a wide range of shapes and sizes.
Strength: Provides high strength-to-weight ratios, suitable for structural applications.
Recyclability: Aluminum is highly recyclable, making it an eco-friendly option.
Cost-Effective: Efficient process with minimal material waste.
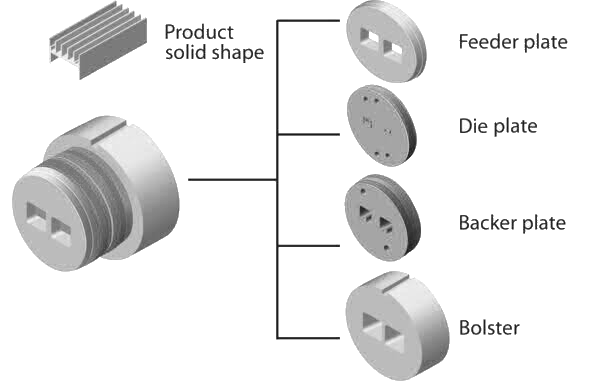
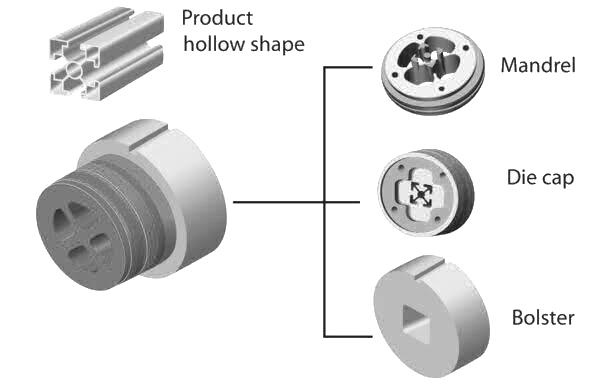
Applications
Aluminum extrusions are used in various applications such as window frames, automotive components, heat sinks, and structural frames. The versatility of aluminum extrusion allows for customized solutions tailored to specific industry needs.