High-Pressure Die-Casting Process
High-pressure die-casting (HPDC) is similar to permanent mold casting except that the metal is injected into the mold under a high pressure of 10-210MPa. This results in a more uniform part with a generally good surface finish and good dimensional accuracy, as well as 0.2 % of the casting dimension. For many parts, post-machining can be totally eliminated, or very light machining may be required to bring dimensions to size.
The main die-casting castings alloys are; zinc, aluminum, magnesium, copper, lead and tin. Every alloy have its suitable type of HPDC. Due to high pressurized process in HPDC a small thickness parts can be produced as 0.8mm in aluminum alloys, 0.6mm in zinc alloys, 1.25mm in brass and bronze alloys, and 1.25mm in magnesium alloys. On the other hand, castings weight in HPDC are limited due to machines capacities. HPDC process have two types, cold-chamber and hot-chamber process.
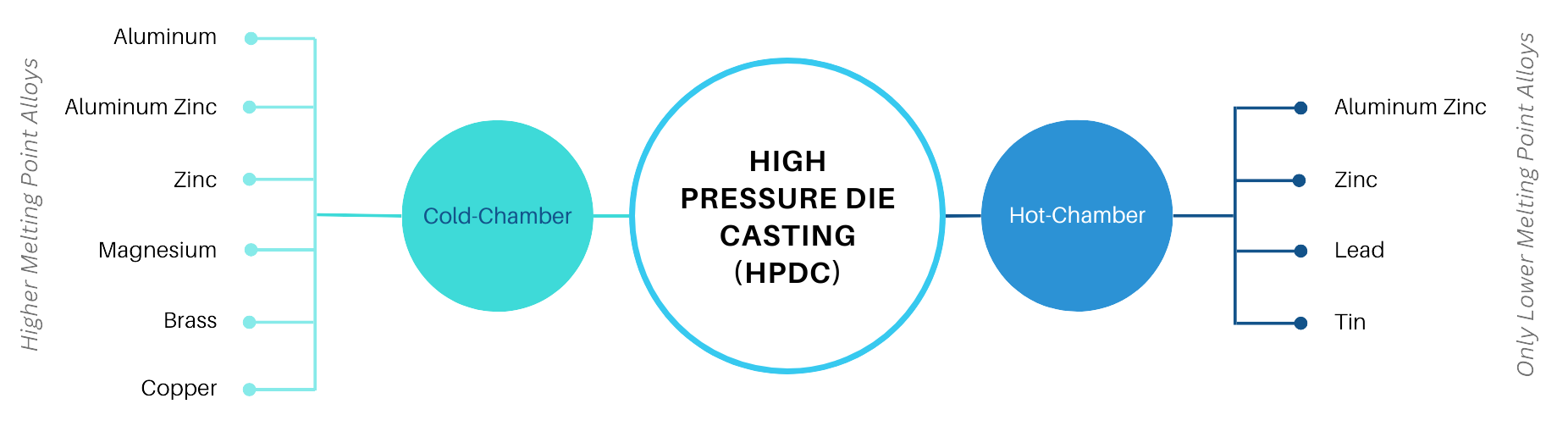
- In a cold-chamber process, the molten metal ladled into the cold-chamber for each shot. There is less time exposure of the melt to the plunger walls or the plunger. This is particularly useful for metals such as Aluminum, and Copper (and its alloys). That alloy easily with Iron at the higher temperatures.
- In a hot-chamber process, the pressure chamber is connected to the die cavity is immersed permanently in the molten metal. The inlet port of the pressurizing cylinder is uncovered as the plunger moves to the open (unpressurized) position. This allows a new charge of molten metal to fill the cavity and thus can fill the cavity faster than the cold chamber process. The hot chamber process used for metals of low melting point and high fluidity such as tin, zinc, and lead that tend not to alloy easily with steel at their melt temperatures.
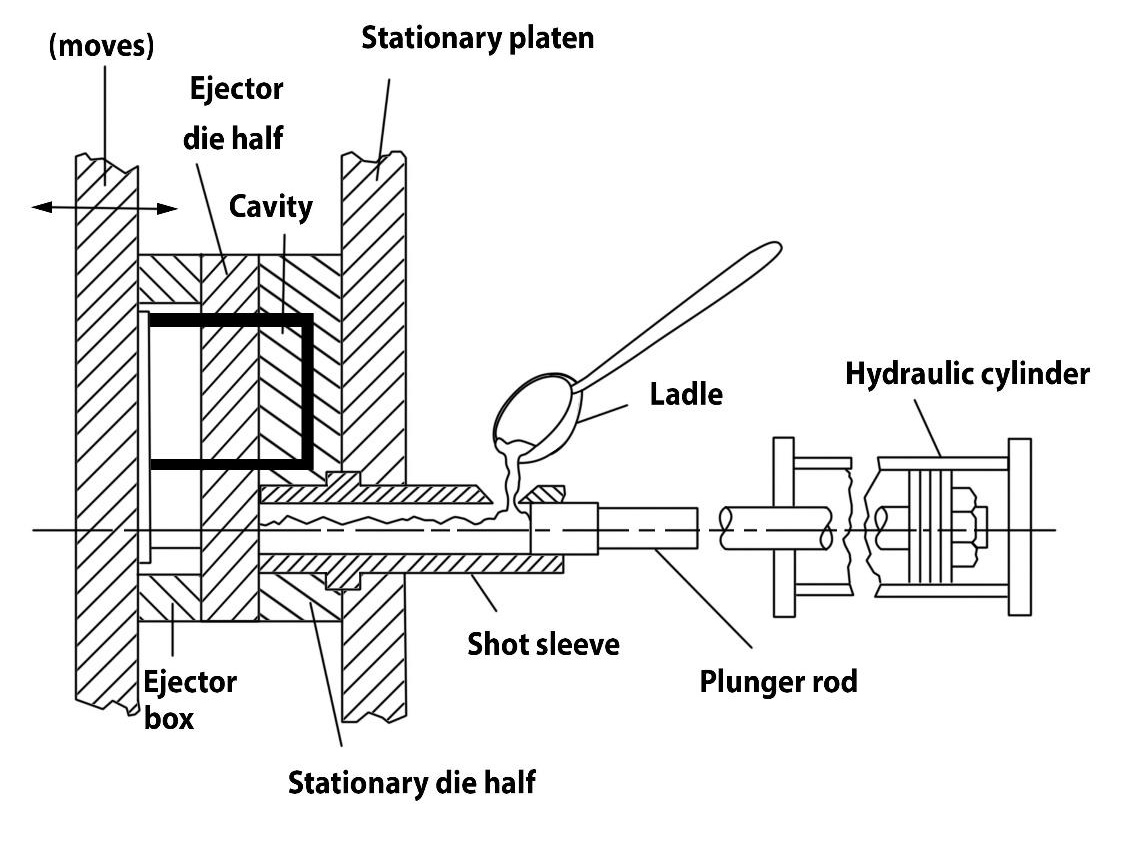
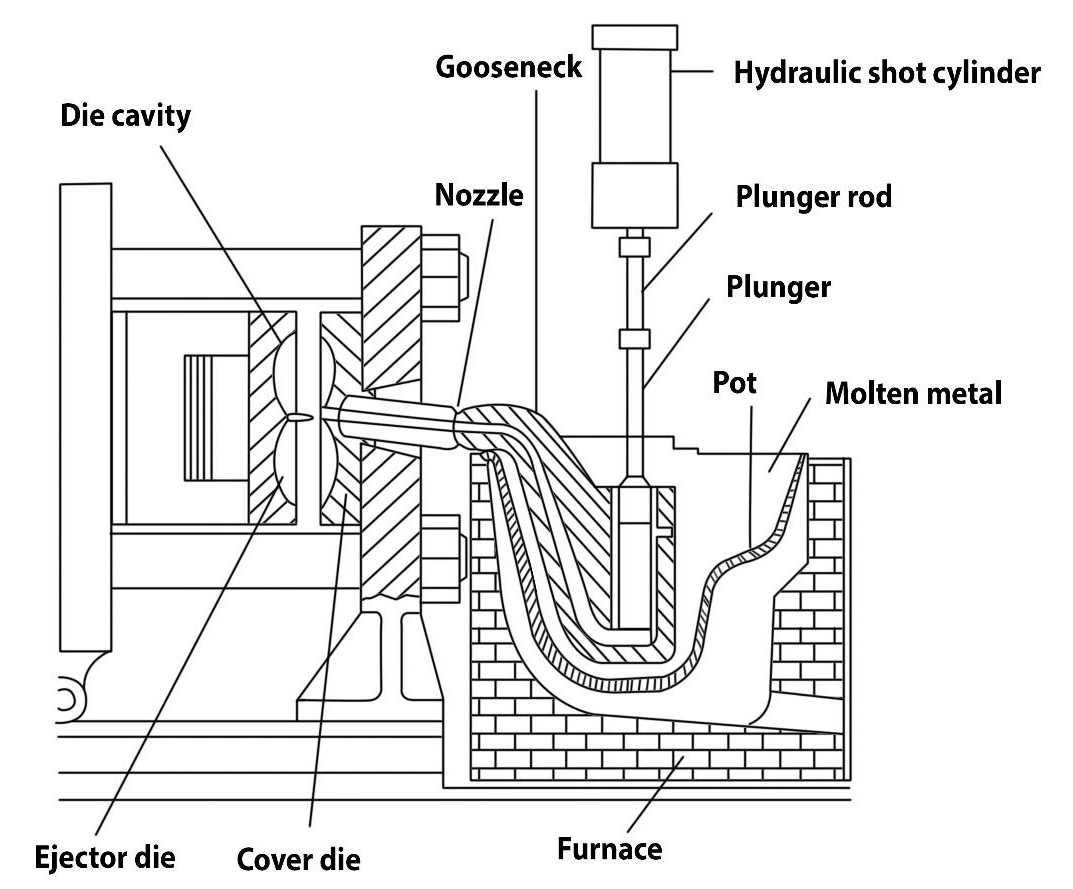
High-Pressure Die-Casting Mold
Die-casting molds (called dies in the industry) tend to be expensive as molds made from hardened steel, moreover the cycle time for building these tend to be long. In addition, the stronger and harder metals such as iron and steel cannot be casted. The die designer identify the parting line that represents the point at which two different sides of a mold come together. The two different sides of the mold called two halves’ (Cover Half – Ejector Half). The cover half is the side that the injected metal comes through, and the ejector half is the side that the part remains on it then ejected after opening by ejector pins.
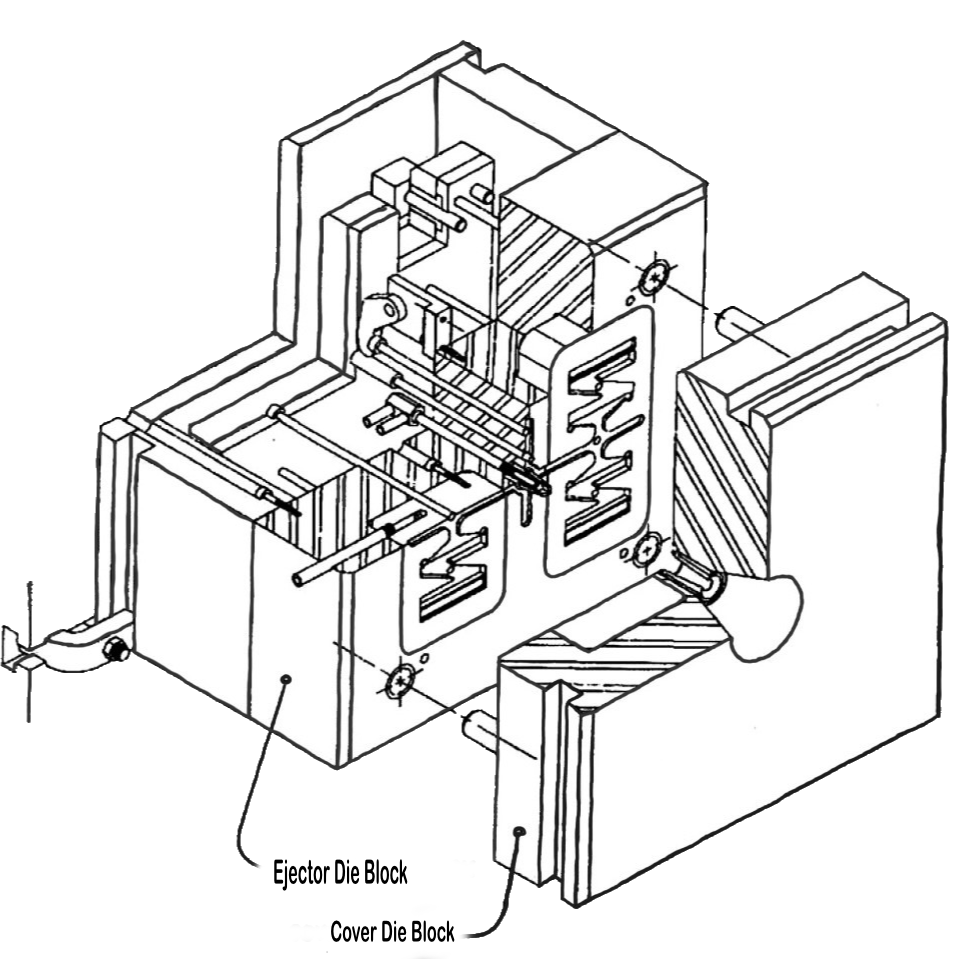
The main shape of the solidified part formed in the matrix part. This matrix contains the negative shape of the part and other helpful shapes for casting process (Runner – Gates – Over Flow – Air Vents). The injected molten metal came sequentially from sprue to runner, gates, cavities, and overflow. The overflow and air vent are responsible to overcome the mixed air with the molten material and air escape to minimize porosity in the required part. The main challenge to the die designer is to build a gating system that suitable for the desired part dimensions to minimize part porosity, which is common in HPDC process. Moreover, the design must take into account the machine specifications (plunger diameter, distance between tie bars, locking force… etc.) as a constrain on his design.
High-Pressure Die-Casting Advantages
- High-speed production can be achieved as the whole process is completely automated.
- Possible to obtain fairly complex castings than that feasible by gravity die casting due to the use of the movable cores.
- Very small thickness can be easily filled as the liquid metal is injected under high pressure.
- Very good surface finish can be obtained and most of pressure die-casting castings can be directly electroplated without any further processing.
- Closer dimensional tolerance and better mechanical properties can be obtained compared to sand casting.
- Very economic for large-scale production.
High-Pressure Die-Casting Disadvantages
- Large capital investment is required to set up a pressure die casting process.
- The die casting machine and tooling costs very expensive.
- It cannot used for large castings, as the casting machine capacity is limited.
- It is not suitable for all materials because of the limitations of the die material and the alloys used must have a low melting temperature.
- Die-casting mold take long time to produce compared to other casting techniques.
- High Porosity is common.